Sydney Civil delivers world first Green Roads trial
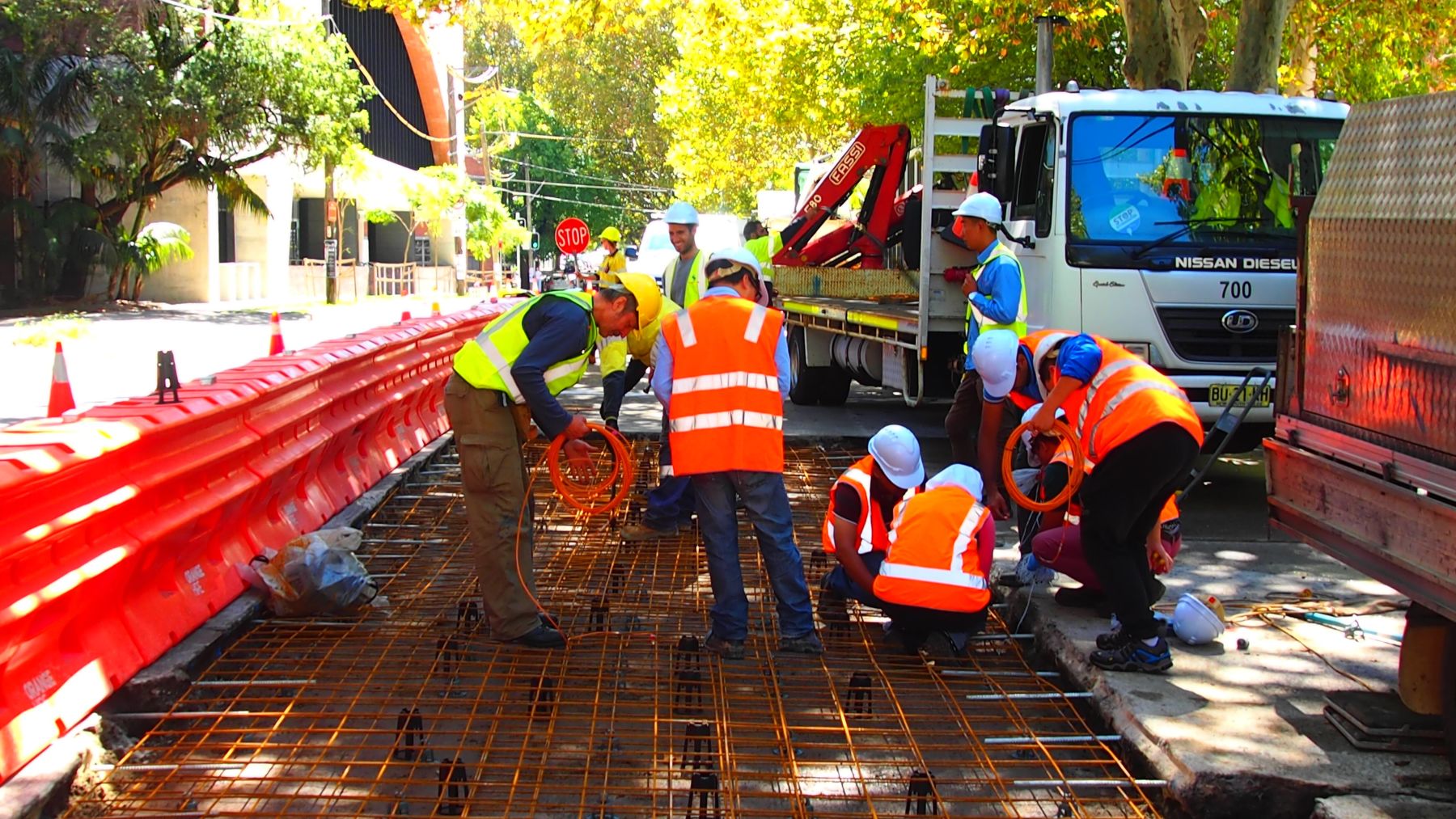
The City of Sydney Council reported recently that they have trialled a new geopolymer material on a major road near Sydney Airport.
In the first trial of its kind, industrial waste from coal-fired power stations and steel manufacturing has been given a new lease on life. Made from fly ash and blast furnace slag, the geopolymer concrete is a sustainable blend of concrete and recycled materials.
This new geopolymer generates just 300kgs of CO2 per tonne of cement, compared to 900kgs from traditional cement production. The carbon emissions savings is equivalent to the electricity used by an average household every 2 weeks.
With 70% of the concrete produced today going into pavements and footpaths, using products like geopolymer concrete for our roads and footpaths has great potential to lower emissions.
Working with researchers from the University of NSW, Sydney Civil in conjunction with the City of Sydney Council have replaced a section of roadway on Wyndham Street in Alexandria to test the green concrete’s durability.
A major road leading to Sydney Airport, Wyndham Street has a high traffic volume which provides the perfect conditions for the trial. Nine sensors have been positioned under the concrete to monitor and compare how the geopolymer concrete performs.
University of NSW researchers and the Cooperative Research Centre for Low Carbon Living will use results from the trial to create the first set of industry guidelines for geopolymer concrete.
Research has been undertaken since the 1990s, but it’s only now this concrete blend is being explored as a product that is not only better for the environment, but also commercially viable. The low CO2 concrete has the potential to put the 400 million cubic tonnes of globally documented waste from the coal and steel industries to good use. While a small amount is currently used in construction, much of it is currently stored on site.
The road’s vital statistics will be monitored for around 5 years, however a lot of the data collected in the first 3 to 12 months of this world-first trial will be used to confirm scientific models and strengthen the UNSW engineer’s predictions.
Professor Stephen Foster, head of UNSW’s school of civil and environmental engineering, is the project lead. He describes the trial as a huge step forward.
“Concrete contributes 7% of all greenhouse gas emissions and in 2018 the world produced about 4.1 billion tonnes of cement, which contributed about 3.5 billion tonnes of CO2. Alternative, low CO2 concrete materials offer potential benefits in reducing the greenhouse gas emissions associated with conventional concrete. This trial is important because we need demonstration projects to accurately assess the performance of geopolymer over time so that there can be broader uptake," said Stephen.
This article was originally published on the City of Sydney’s website.