Extending the life of your formwork with proper form care
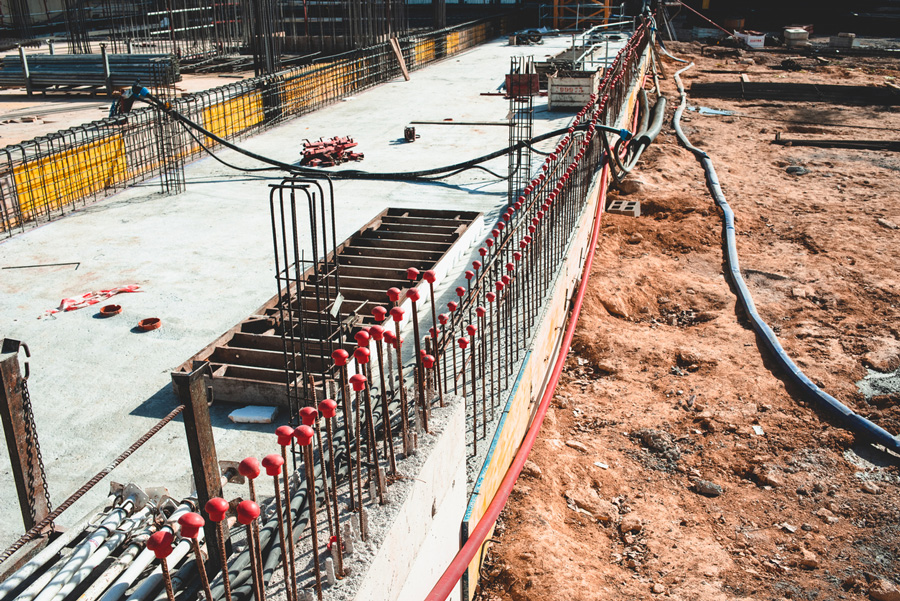
Formwork is a major investment for builders and concreters. A key tool of the trade, formwork is routinely subjected to really tough environments and heavy duty use. Regardless of whether you use plywood, fibreglass, aluminium, steel, urethane or a product like Pecafil it’s an asset you’ll want to take care of.
Taking care of your forms now saves money down the track when damaged or unusable formwork has to be replaced. Additionally, taking good care of formwork will result in less time and effort rectifying problems in finished concrete surfaces if forms aren’t adequately prepared and released cleanly.
An important aspect of form care is the use of a good release agent. Release agents fall into a handful of different categories, but in all cases, proper application is the key to producing the best concrete finish.
Types of form release agents
Release agents are formulated to provide a barrier between the formwork and the freshly poured concrete. They are either a barrier type – a product that simply sits in a layer to separate the concrete and the form – or, they make use of a chemical reaction with the concrete itself. These reactive types contain compounds that react with ingredients of the concrete such as lime, creating a slippery film in between the form and the concrete surface. Other agents are a mix of the two, providing both a barrier and a chemical reaction.
Barrier type release agents include natural formulations like Lanotec, which is derived from lanolin. Diesel and grease formwork release agents also form a barrier, however they can sometimes cause surface voids, staining, or a lower quality appearance. As they are highly viscous, they can take longer to apply and often cannot be sprayed.
Conversely, reactive release agents are easily applied in a thin film by spraying or brushing. These release agents are more likely to produce stain-free concrete surfaces. They often also allow the form to strip more cleanly which saves on clean up. However, the chemical reactions at play can release VOC’s (volatile organic compounds) into the atmosphere.
Low VOC Form Release Agents
VOC’s harm the environment by causing ozone when they react with sunlight. Many countries have followed in the footsteps of the US’s EPA rulings in the 90’s that sought to limit VOC content in coatings such as form release agents.
Nowadays, it is common practice to choose the most environmentally sound product available, so many concreters and precast companies routinely choose low VOC products. The VOC content (or lack thereof) of the form release agent may also be a deciding factor if Green Building Council requirements are specified in your project.
Extensive research and development by companies such as Sika and Dayton have resulted in the best of both worlds: effective reactive agents that contain minimal amounts of VOCs.
How to apply form release agent
Spraying is probably the most efficient and even method of applying form release agent. Using quality spray equipment, an extremely thin film can be applied to large areas, resulting in a consistent application and minimal wastage. Although thin chemically reactive release agents can appear more expensive, often they provide more coverage and are therefore as economical as grease or barrier type products.
Other ways of applying form release agent include using a sponge or rag to wipe the product onto the forms, or in large scale facilities such as precast operations, dipping the forms into the agent may be used. Some agents are brushed onto forms, although as this is a manual process, the consistency can be hard to control.
Looking after your formwork
Protecting your forms when they are not in use makes good economic sense. Forms will last longer when properly cared for, which includes protecting them from rust or corrosion in the case of metallic forms. In this case rust inhibitors can be useful.
Protecting forms whilst in storage can sometimes be achieved with a coating of grease, diesel, or release agent. However, a heavy handed or repeated application can end up damaging the forms. How easy the grease is to remove should also be taken into account.
At the end of the day, formwork is a major investment and it makes sense to extend the life of your assets as much as possible.